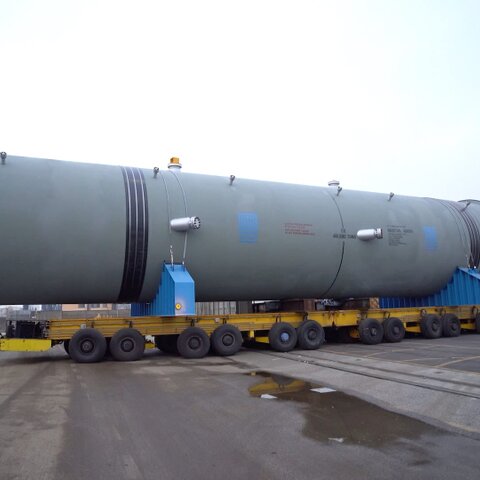
Manufacturer of heavy equipment for the Oil & Gas industry
For over half a century, the Oil and Gas division of ATB Group has been offering know-how and production capacity to the world's leading petrochemical companies.
Oil and natural gas touch our lives in countless ways every day. More than 60 percent of our daily energy needs is supplied by hydrocarbons and gas, keeping us warm in cold weather and cool in hot weather, cooking our food and heating our water, generating our electricity, and powering our cars, buses, trains, ships and planes.
ATB Group is an international designer and manufacturer of process equipment for the Oil and Gas industry, a specialist in ammonia and urea production plants, petrochemical plants and gas treatment plants.
Innovation, diversification and research of new markets are our guidelines.We create new collaborative business models, by establishing relationships with partners, suppliers and customers, and leveraging our worldwide sales network.
Associate member of AIPE (Italian Association of Pressure Equipment)